Created a CAD model with Autodesk Fusion360, optimizing for durability, ease of repair, and weight reduction. Designed human-like fingers and a robust thumb with increased degrees of freedom.
ABS (Acrylonitrile Butadiene Styrene) was used for its durability and lightweight properties, resulting in a 22% volume reduction from the initial Proof of Concept phase.
Parts were 3D printed and fabricated in the institute’s central workshop, ensuring precision and customization.
Integration of Arduino Nano RP2040 Connect, sEMG (Surface Electromyography) sensors, a 16-channel servo motor controller, high-torque servo motors, tactile sensors, and haptic motors. Strategic positioning of sEMG electrodes to detect muscle activity and transmit signals to the Arduino for processing. Computations, sensory data collection, and motor commands managed using Arduino Nano RP2040, selected for its inbuilt Wi-Fi and Bluetooth capabilities.
Development of a custom neural network algorithm in C++ to process muscle signals and control finger actuation, utilizing a dataset of approximately 2200 data points to distinguish between active and passive arm positions.
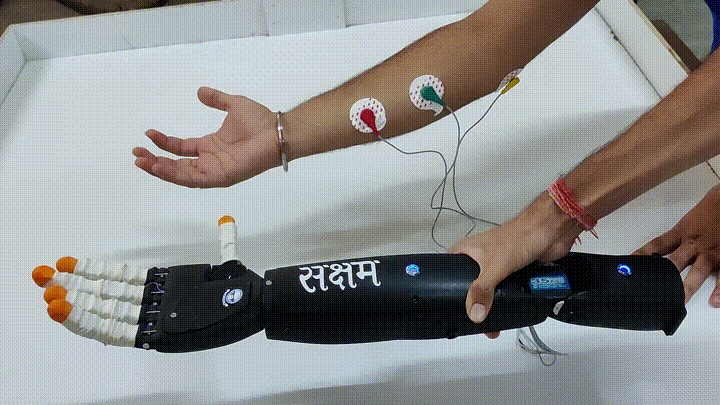
Creation of a user-friendly web application for testing and controlling the prosthesis, allowing individual or combined finger actuation. IoT enabled for data collection, performance monitoring, and potential over-the-air updates to enhance the neural network and functionality.